Technical processes
We can do almost anything. Our extensively qualified employees are proficient in a wide range of sheet metal processing methods. If you have a very specific requirement, we can call on our network of partner companies in the local area.
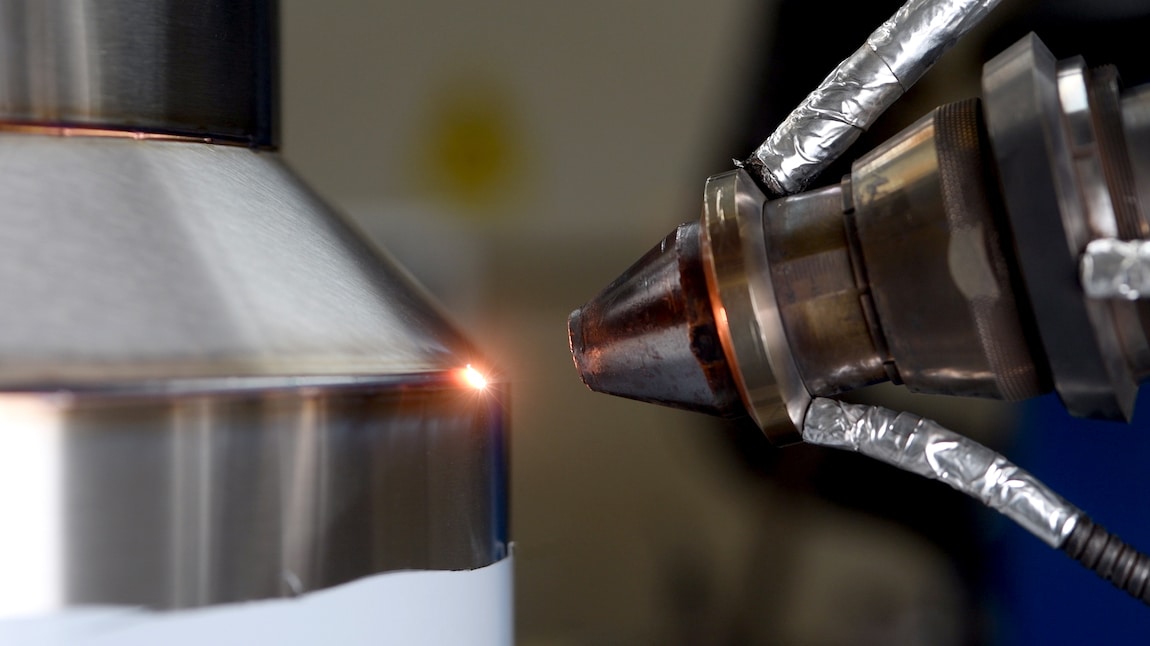
Laser cutting: large formats up to 1500 x 3000 mm and 20 mm material thickness.
Punch-laser combination: large formats up to 1500 x 3000 mm and 8 mm material thickness using punching, thread forming, louvers forming, nibbling, beading, roller beading tool
Roll levelling: up to 1500 mm in width and 12 mm material thickness
Roll bending: up to 2000 mm in width and 6 mm material thickness
Bending: CNC bending up to 3000 mm in width and 15 mm material thickness
Laser Welding: CNC-controlled 3D-laser welding with 8 axes
WIG or MIG welding: including forming
Longitudinal seam welding: up to 2500mm
Grinding pattern production: by hand or using a dual-belt grinding machine up to 400 grain
Components: finishing up to 3,000mm in length
Industrial grinding: up to 1,500mm in width
Assembly of mechanical, hydraulic, and pneumatic modules and system components, including cabling.
Assembly and inspection of control systems
Ready-to-plug-in devices
In-House electrical inspection is possible
Repair of your processing vessels/pressure vessels on site
The Kasto automatic saw cuts all solid and hollow materials cleanly and precisely at the desired miter angle.
Machines
For our strong material and complex geometries, we not only have the right touch, but also an extensive, modern machine park.
Compact, robust automatic full-sawing machine in a stable design with swivel joint. We use it to cut solid, shaped and hollow materials in all material qualities. This also includes stainless steel and titanium. We saw individually or in bundles.
Our blank straightening machine reliably stress relieves and straightens sheet metal and parts blanks. The subsequent production processes benefit from this.
The innovative CoolLine equipment combined with a powerful TruFlo 5000 laser makes our laser from Trumpf the optimal tool for strong materials and complex geometries. With it, we can contour stainless steel up to 20 mm so precisely and cleanly that the webs between the sheet metal parts turn out very thin. This saves material and increases the quality of the product.
When the demands on quality, productivity and flexibility are very high, the TruMatic 7000 is in demand. This new punch laser performs numerous forming operations with automatic tool change. It punches all hole patterns from 0.8 millimetres. This opens up many possibilities: It can be used as a cup, pull-through, punching and embossing tool and to form threads and ventilation gills (fixed and endless).
Thickness: up to 8,0 mm Steel, Stainless Steel, Aluminium
Format: up to 1500 x 3000 mm
Thread forms: M3 to M8
This manually operated deburring machine is suitable for grinding, deburring, rounding edges and polishing – on a variety of materials. The grinding head with two rotating grinding wheels is mounted on a swivel arm. The speed of the machine is infinitely variable. It has a vacuum table system to hold blanks and workpieces in place. With the swivelling sanding head, we can process all edges precisely.
DIN says that there is no such thing as scratch-free. Nevertheless, we do our utmost! We protect sensitive surfaces with care during the production process and apply original protective films wherever possible. These foils accompany the entire production process up to final assembly and to the customer. It doesn’t get any better than this.
These three swivel bending machines are ideal for bending flat sheets that are to be formed at the edge or in the surface. During bending, the sheet metal remains on the machine’s hold-up system. The operator does not have to hold the weight or lift the sheet during bending. This allows him to handle even large and heavy sheets alone and the machine works particularly precisely.
In die bending and folding, the sheet is bent by a controlled downward movement of the press beam. These machines press the flat sheet with an upper tool into a V-shaped lower tool (die). This forms it in a straight line. The back gauges ensure that a workpiece is positioned exactly. And the laser-guided control of the angles guarantees the highest precision during bending.